Metal is without doubt one of the most helpful supplies on the planet. A spine of contemporary life, it’s utilized in skyscrapers, automobiles, airplanes, bridges, and extra. Sadly, steelmaking is a particularly soiled course of.
The most typical manner it’s produced entails mining iron ore, decreasing it in a blast furnace by means of the addition of coal, after which utilizing an oxygen furnace to burn off extra carbon and different impurities. That’s why metal manufacturing accounts for around 7 to 9 percent of humanity’s greenhouse fuel emissions worldwide, making it one of many dirtiest industries on the planet.
Now Boston Steel is looking for to scrub up the steelmaking business utilizing an electrochemical course of referred to as molten oxide electrolysis (MOE), which eliminates many steps in steelmaking and releases oxygen as its sole byproduct.
The corporate, which was based by MIT Professor Emeritus Donald Sadoway, Professor Antoine Allanore, and James Yurko PhD ’01, is already utilizing MOE to get well high-value metals from mining waste at its Brazilian subsidiary, Boston Steel do Brasil. That work helps Boston Steel’s group deploy its expertise at business scale and set up key partnerships with mining operators. It has additionally constructed a prototype MOE reactor to provide inexperienced metal at its headquarters in Woburn, Massachusetts.
And regardless of its identify, Boston Steel has international ambitions. The corporate has raised greater than $370 million so far from organizations throughout Europe, Asia, the Americas, and the Center East, and its leaders anticipate to scale up quickly to remodel metal manufacturing in each nook of the world.
“There’s a worldwide recognition that we have to act quickly, and that’s going to occur by means of expertise options like this that may assist us transfer away from incumbent applied sciences,” Boston Steel Chief Scientist and former MIT postdoc Guillaume Lambotte says. “Increasingly more, local weather change is part of our lives, so the stress is on everybody to behave quick.”
A decades-long search
Because the Nineteen Eighties, Sadoway had carried out analysis on the electrochemical course of by which aluminum is produced. The main target of the analysis was to discover a substitute for the consumable anode utilized in that course of, which makes carbon dioxide as a by-product. Throughout that work, he started to conceptualize the same electrochemical course of to make iron, the precursor to metal.
But it surely wasn’t till round 2012 that Sadoway and Allanore, then a postdoc at MIT, found an iron-chromium alloy that might function an inexpensive sufficient anode materials to make the method commercially viable and produce oxygen as a byproduct. That is when the pair partnered with James Yurko, a former pupil, to discovered Boston Steel.
“The entire elementary research and the preliminary applied sciences got here out of MIT,” Lambotte says. “We spun out of analysis that was patented at MIT and licensed from MIT’s Expertise Licensing Workplace.”
Lambotte joined the corporate shortly after Sadoway’s group printed a 2013 paper in Nature describing the MOE platform.
“That’s when it went from the lab, with a espresso cup-sized experiment to show the basics and produce a number of grams, to an organization that may produce a whole bunch of kilograms, and shortly, tons of metallic,” Lambotte says.
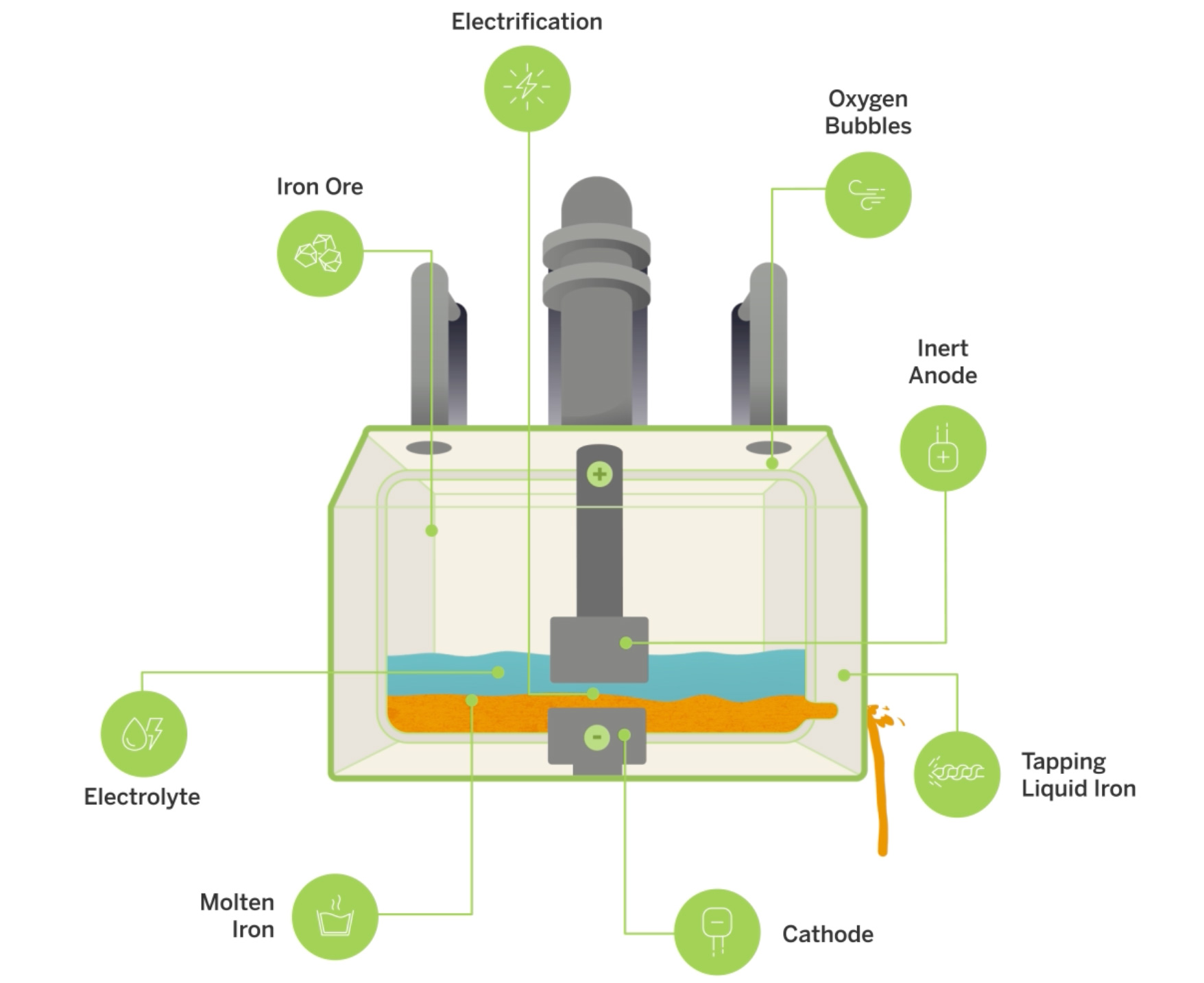
Boston Steel’s molten oxide electrolysis course of takes place in modular MOE cells, every the dimensions of a faculty bus. Iron ore rock is fed into the cell, which incorporates the cathode (the adverse terminal of the MOE cell) and an anode immersed in a liquid electrolyte. The anode is inert, that means it doesn’t dissolve within the electrolyte or participate within the response aside from serving because the constructive terminal. When electrical energy runs between the anode and cathode and the cell reaches round 1,600 levels Celsius, the iron oxide bonds within the ore are break up, producing pure liquid metallic on the backside that may be tapped. The byproduct of the response is oxygen, and the method doesn’t require water, hazardous chemical compounds, or precious-metal catalysts.
The manufacturing of every cell depends upon the dimensions of its present. Lambotte says with about 600,000 amps, every cell might produce as much as 10 tons of metallic every single day. Steelmakers would license Boston Steel’s expertise and deploy as many cells as wanted to achieve their manufacturing targets.
Boston Steel is already utilizing MOE to assist mining corporations get well high-value metals from their mining waste, which normally must endure pricey therapy or storage. Lambotte says it is also used to provide many different kinds of metals down the road, and Boston Steel was not too long ago chosen to barter grant funding to provide chromium metallic — essential for a lot of clear vitality purposes — in West Virginia.
“In case you look world wide, numerous the feedstocks for metallic are oxides, and if it’s an oxide, then there’s an opportunity we are able to work with that feedstock,” Lambotte says. “There’s numerous pleasure as a result of everybody wants an answer able to decarbonizing the metallic business, so lots of people have an interest to know the place MOE matches in their very own processes.”
Gigatons of potential
Boston Steel’s metal decarbonization expertise is at the moment slated to achieve commercial-scale in 2026, although its Brazil plant is already introducing the business to MOE.
“I feel it’s a window for the metallic business to get acquainted with MOE and see the way it works,” Lambotte says. “You want individuals within the business to understand this expertise. It’s the place you kind connections and the way new expertise spreads.”
The Brazilian plant runs on one hundred pc renewable vitality.
“We will be the beneficiary of this large worldwide push to decarbonize the vitality sector,” Lambotte says. “I feel our strategy goes hand in hand with that. Totally inexperienced metal requires inexperienced electrical energy, and I feel what you’ll see is deployment of this expertise the place [clean electricity] is already available.”
Boston Steel’s group is happy about MOE’s software throughout the metals business however is concentrated before everything on eliminating the gigatons of emissions from metal manufacturing.
“Metal produces round 10 p.c of world emissions, so that’s our north star,” Lambotte says. “Everyone seems to be pledging carbon reductions, emissions reductions, and making web zero objectives, so the metal business is basically trying onerous for viable expertise options. Individuals are prepared for brand new approaches.”